中國冶金報 中國鋼鐵新聞網
江飛 報道
黃智強 李立峰 攝影
走進智慧鋼城
近年來,鋼鐵行業持續推進高質量發展,在邁向“鋼鐵強國”的征程上,數字化與智能化結合的“智慧”正成為鋼鐵產業的鮮明特征。數字化、智能化改變的不僅僅是生產線,更重要的是它在改變生產方式的同事,也改變了生產的理念,這正是目前傳統制造業正在追尋的發展路徑。
2020年底,工業互聯網專項工作組印發《工業互聯網創新發展行動計劃(2021-2023年)》,明確通過對人、機、物全面連接,變革傳統制造模式、生產組織方式和產業形態,構建起全要素、全產業鏈、全價值鏈全面連接的新型工業生產制造和服務體系。從2020年到2021年全年,鋼鐵行業智慧制造和5G技術開始與產線加速融合,快速推進,智能工廠在鋼鐵行業已逐步成為標配目標。
近年來,永鋼集團大力實施智能化改造,通過互聯網、大數據等新技術與生產制造的深度融合,全面提升設備自動化、數字化水平,全力打造具有“智慧”的新型鋼廠。
以“智”促“質”,催生企業發展新動能
《中國制造2025》中明確指出“推進制造過程智能化”。永鋼利用智能感知、人機交互、機器人、多工序的關聯優化技術,對生產車間現有裝備進行全面優化,實現裝備從自動化向智能化轉變、供應鏈從局部優化到全局優化的轉變,進一步提高工藝技術水平和裝備自動化水平。
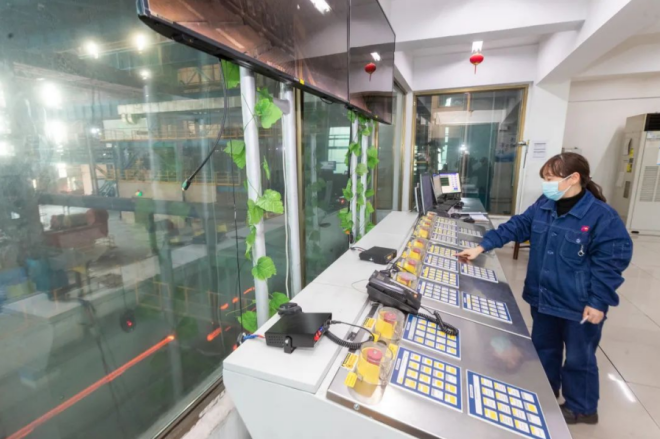
煉鋼集中控制室
在永鋼煉鋼三分廠,“人工煉鋼”逐步式微,“智能煉鋼”正漸漸扛起大梁。長期以來,在轉爐生產過程中,一直受限于每位操作人員的操作水平和判斷經驗,往往會導致鋼水成分出格、成分波動較大、人工添加合金不精準等問題出現,使得最終生產指標與原定預期值產生偏離。2019年起,永鋼成立“合金加料模型”攻關小組,歷時一年成功完成了合金加料模型項目的研發。
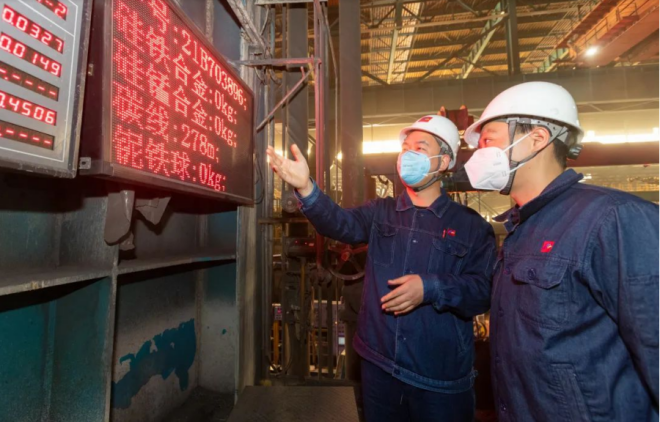
合金加料模型應用
“合金加料模型”介入生產后,有效控制鋼水收得率,準確預估出鋼量,將偏差由原先的3噸左右縮小到了平均1.96噸以內;在內控標準的基礎之上,還實現了對合金添加提供精準指導,為煉鋼提供可靠的加料指導,減少爐次之間鋼種成分的波動,有效提升不同批次產品的質量和穩定性。
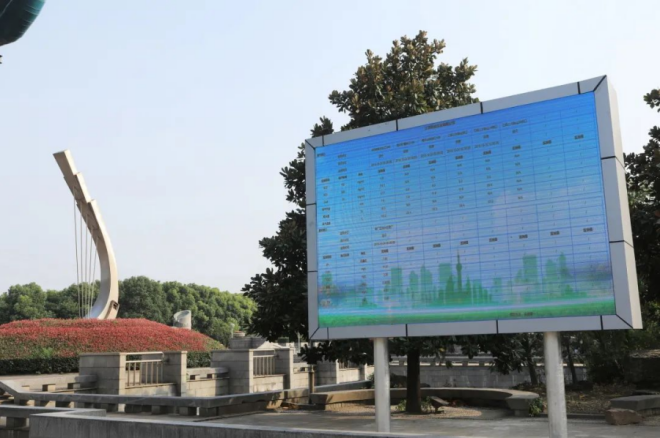
大屏顯示大氣在線監測數據
智能制造,鍛造綠色發展強引擎。為集中控制監控儀的運行排放情況,及時對廠區及周邊廢水、廢氣、揚塵情況及環境空氣質量進行監測和預警,永鋼打造了環境監控一體化平臺。二氧化硫指標正常、氮氧化物指標合規……污染物的自動監控數據、環境行為評定結果、環境空氣質量等數據信息在LED顯示屏上便可一目了然。在燒結機頭、機尾,球團焙燒等主要污染物排放口安裝了共52套污染源自動監控設施以及12個高清視頻監控,并利用環境監控一體化平臺,將污染物的自動監控數據、環境行為評定結果等數據信息在LED顯示屏上進行公示、公開,接受社會監督。
以“數”提“速”,驅動產業管理新模式
在數字化轉型深化推進的形勢下,數字技術與鋼鐵行業不斷融合,正在加速推動鋼鐵企業管理與生產的變革與重構。永鋼堅定走好數字化轉型之路,用數字化賦能價值創造,提升存量,拓展增量,推動企業高質量發展。
2021年,永鋼建立了一個快速、有效、標準化的能源管理系統,對已有設備、生產系統、二級系統、成本與產量系統等數據進行集成,并對全廠的能源計量點進行梳理規范,聯通“信息孤島”,建立起統一的能源數據信息共享庫,實現了從基于信號控制到基于信息控制的轉變。數據共享、數據同源后,大大減輕了運維人員的工作量,提高了數據的一致性及傳輸效率,為能源精細化管理提供了有效支撐。

能管中心
“從預警到解決問題,前后不超過1個小時?!爆F在,能管中心操作員接收到“球團高爐煤氣溫度高于80℃”的報警推送信息后,可以快速定位問題癥結,隨即聯系到相關負責人組織排查。EMS能源管理系統通過對公司過往水、電、煤氣等能耗數據的統計分析,設定一個標準值,生產線上能耗如果大幅超標,系統就會及時示警,有效地指導生產,提高生產效率。
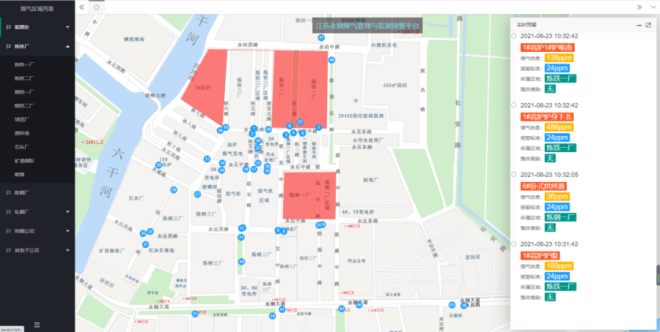
廠區內煤氣區域總覽
此外,永鋼還打造了“煤氣管理與預警監測平臺”,基于PHP框架開發,采用HTML5、CSS等網頁技術、網絡通信技術,可以有效監測全廠區煤氣實時動態情況。廠區內每個需要監測煤氣含量的區域內,都安裝了煤氣監測器,實現與煤氣監測預警平臺的實時相連。煤氣監測器每隔15秒便向平臺上報一次煤氣含量數據,數據會在后臺自動保存,形成煤氣信息專屬數據庫,方便后期追溯,實時保障安全生產。
“數”以“智”用,賦予智能制造新活力
在制造型企業,車間處于非常重要的位置,很大程度上,車間強則企業強,車間智則企業智。目前,永鋼已有智能煉鋼生產車間、電爐大棒智能生產車間、精品線材智能生產車間、智能煉鐵車間4個江蘇省智能制造示范車間。
你能想象嗎?如今,買鋼筋像買菜一樣方便,這在永鋼就可以實現,不僅能按需買還能按需“種”。
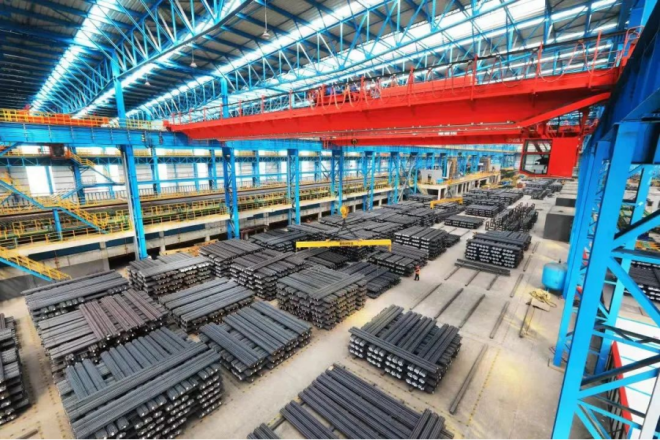
棒材生產車間
“叮咚!”永鋼云商平臺上跳出一個新訂單——采購一批特種合金棒材。無論客戶身處何方,只需登錄平臺,即可按需下單。為此,永鋼開發實施“特種合金棒材全流程智能化改造升級項目”,打造了全價值鏈運營及協同研發平臺、網絡協同可視化制造平臺和制造全流程節能及安環管控平臺。
依托全價值鏈運營及協同研發平臺,永鋼根據客戶需求制定個性化生產方案,智能生成原材料采購、生產排期計劃等。全流程智能化從客戶發布需求或下單的那一刻便開始了, 當客戶需要一款全新產品時,平臺將自動推演研發進度等,全方位保障客戶權益。
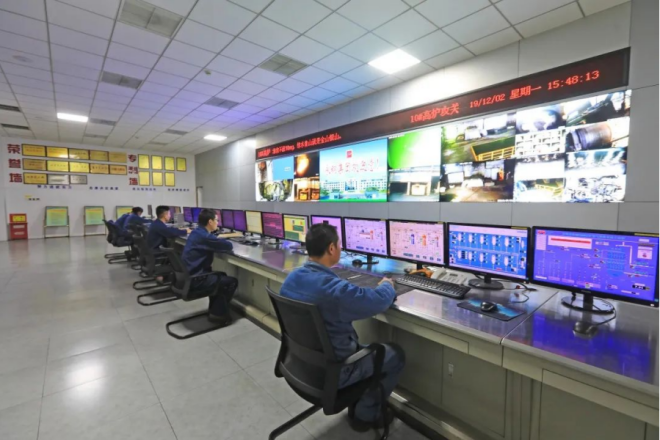
生產控制
當特種合金棒材開啟生產之路,“沿途”所有車間的智能化平臺便已經準備好了。從配料到半成品,再到最終的成品,網絡協同可視化制造平臺將統領智能生產全局。特種合金棒材存在品種多、批量小的特點,過去,永鋼在生產過程中往往面臨著排產計劃性差、質量穩定性不高、資源利用率低等問題。為此,永鋼基于工序仿真模型建立了標準化工藝管理平臺,構建面向全流程預測、優化、決策的大數據平臺等,全面建立起網絡協同可視化制造平臺。
依托智能生產裝備及大數據分析應用,該平臺構建起覆蓋生產、物流、質量、設備運維的全計劃編制,優化了工藝路線,實現生產設備狀態、生產運行情況的全流程可視化監控及數據全追溯,確保了產品質量的穩定性。
一直以來,永鋼集團以高標準嚴要求踐行綠色發展理念,這一基因也始終融入在特種合金棒材的生產全流程中。在這一產品的誕生之路上,全新打造的節能及安環管控平臺發揮了積極作用。
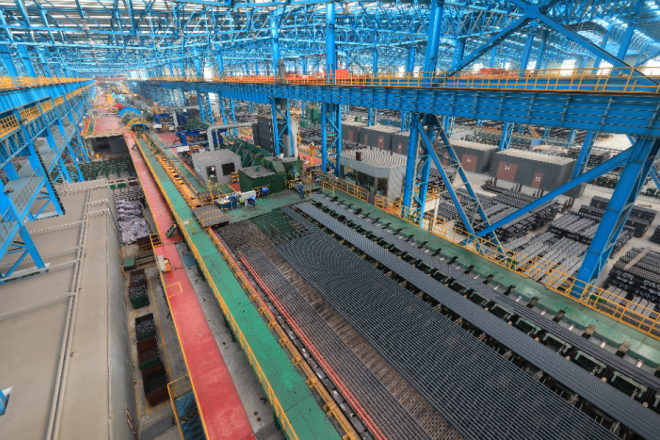
生產流程
以全廠超低排放一體化管控治平臺為例,將生產設備、監測設備、治理設備等運行數據、重點區域視頻監控等信息接入平臺,料場大棚通過鷹眼、視覺粉塵監測系統,自動與霧炮聯動,通過記錄治理設施和對應生產工藝設備或產塵過程同步運轉情況,實現一屏看全廠、一鍵治超標、一網管超排,達到超低排放A級企業標準,打造首家省級超低排放智能化示范企業。

綠色工廠
此外,該平臺還建立了能源管控及優化系統、安全生產信息化管控系統以及環境監測與監控系統,有效降低了整廠生產能耗波動、減少能源浪費,企業安全生產管理水平進一步提升。
2021年,“特種合金棒材全流程智能化改造升級項目”獲批江蘇省智能制造示范工廠建設項目,成為永鋼數字化轉型邁上新臺階的有力見證。
“十四五”期間,永鋼將在建成4個省級示范智能車間的基礎上,加快智能物流、智能倉儲、工業機器人等智能制造項目落地,并以鋼鐵行業為依托、面向傳統裝備制造業,打造一家國內外領先的智能制造解決方案供應商?!暗健奈濉冷摿帉崿F產業鏈高效協同、數據智能、數字化驅動融合創新,把鋼鐵生產制造基地打造成一流的數字化、信息化、智能化的江蘇省智能工廠?!庇雷靠毓煽偛?、永鋼集團總裁吳毅介紹。