本報通訊員 李偉 記者 孟祥林
9月20日早上,換好工作服的倒班作業長江滔走進釩氮合金智能化中控室,通過察看大屏幕數據顯示和視頻畫面,釩氮合金智能制造示范性產線的運行情況及主要指標變化情況一目了然。他到現場確認完畢后,快速返回中控室,組織召開了班前會,對當班任務進行了分工,交代了注意事項,整個過程不到20分鐘。這是釩氮合金產線智能化改造前至少要花一個小時才能完成的工作。
鞍鋼集團攀鋼集團首批兩化融合示范線建設項目——釩鈦資源股份有限公司(下稱“攀鋼釩鈦股份”)釩氮合金兩化融合示范線建設項目(此為申報前采用的項目名稱),成功融合了信息、制造、控制、通信、人工智能和5G等先進技術,并率先在國內釩制造領域實現了智慧物聯傳輸、生產物料自主運轉、產品自動包裝、全線集中遠控和物流連續自動等功能,是國內第一條釩氮合金數字化生產線。2023年11月份,該項目入選2023年度智能制造優秀場景。
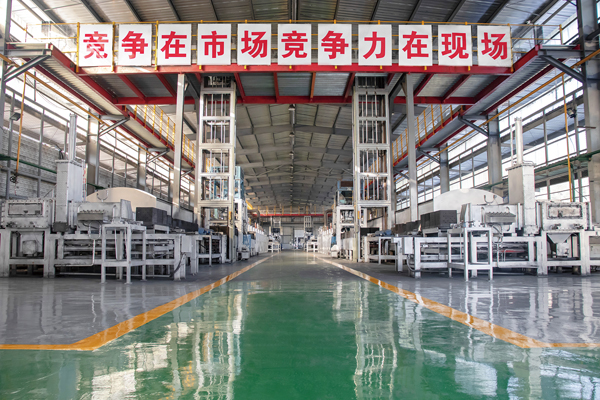
圖1 產線內景
釩氮合金主要用作含釩微合金鋼添加劑,微量加入就能顯著改善鋼材的綜合力學性能和焊接性能,是目前釩產品市場的主流產品之一。但因其生產工藝復雜,生產條件要求高,2018年以前,國內還沒有釩氮合金生產企業做過全流程自動化、智能化生產方面的嘗試。
攀鋼釩鈦股份下屬攀枝花釩制品分公司擁有在世界釩制品生產企業中處于領先地位的釩氮合金完整生產線。但由于產線建設時間較早,受場地和技術條件限制,各工序離散作業、自動化程度低、缺乏過程控制、人工作業環節多、勞動強度大、生產現場環境差,產品信息全靠人工記錄和紙片傳遞,設備故障排查時間長,生產過程質量追溯難以開展,建設釩氮合金智能化產線具有重要的探索意義。
2018年初,攀鋼立項實施釩氮合金兩化融合示范線建設項目。攀鋼集團旗下成都星云智聯科技有限公司作為項目總承包方,與攀鋼相關單位攜手,按照“整體策劃,分步實施”的工作思路,從技術設計、功能實現、方案實施等方面開始了大膽探索。
2019年下半年,隨著機械臂自動卸料裝置、無人吊車、AGV叉車和自動包裝線等智能化設備,以及配套的5G信息化、物聯網等系統陸續在攀枝花釩制品分公司釩氮合金生產線投用,釩氮合金的傳統生產方式逐步改變。
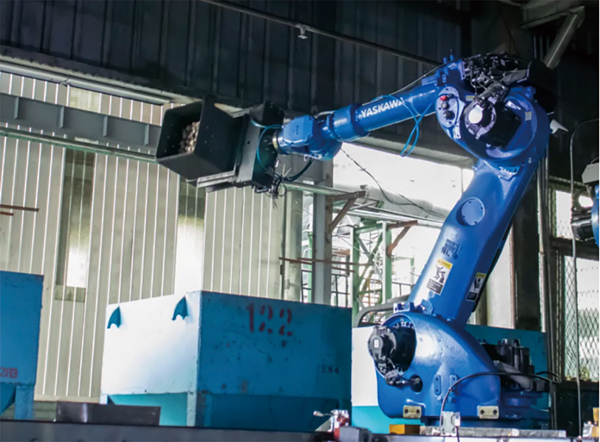
圖2 機械臂卸料
2020年,機械臂卸料裝置的穩定運行,結束了攀鋼集團釩氮合金煅燒工序生產全靠人工上卸料、搬坩堝的歷史;智慧物聯傳輸系統打通了生產過程中的物流斷點,實現了釩氮合金生料球和成品的物流自動運轉和集中控制;生產可視化系統對主要工藝參數、人員生產行為、設備在線狀態數據進行了采集、存儲、分析,對異常情況及時報警并集中顯示,基本實現了即時調度和責任追溯等功能,有效減少了事故停機、事故擴大化等情況;生產過程控制系統緊密結合MES(制造執行系統)建設,通過對各單元生產數據的實時自動收集和高效準確傳遞,實現了各生產工序間的橫向及縱向信息集成,基本實現了工藝過程控制自動化;生產物料自主運轉系統配套無人吊車、AGV叉車等智能設備,實現了生產物料的自動轉運;產品自動包裝線建成投用后,實現了釩氮合金產品的自動破碎、輸送、稱量和封口等功能。
一系列自動化、智能化裝備及5G技術陸續在攀鋼釩鈦股份攀枝花釩制品分公司生產現場落地生根,讓釩氮合金產線的作業模式和生產環境發生了巨大變化,煥發出勃勃生機。
“未實施智能化改造前,我們在釩氮合金生產過程中,全靠人工進行上卸料、配料及物料倒運和包裝等操作,勞動強度大。尤其是在煅燒工序,單個石墨坩堝裝滿生料球后,重達60公斤以上,全靠人工搬運,同時還要注意灑落在地上的石墨細粉,稍不留神就會腳下打滑,職工們干活都是弓著身子,小心翼翼地挪步,每天都是灰頭土臉、汗流浹背。如今,職工在集成控制室中,就能清晰地掌握現場生產過程的重要控制參數變化和物料轉運情況,及時發現設備故障,避免事故擴大化,生產作業效率得到明顯提升,現場作業環境也得到極大改善,靠人工搬運坩堝、弓著身子在煅燒現場來回‘溜冰’的日子徹底成為歷史。”全程參與了釩氮合金兩化融合示范產線建設的攀枝花釩制品分公司釩氮產線技術員唐琪對改造前后的變化深有感觸。
攀鋼釩鈦股份本身就擁有多項釩氮合金核心生產技術,近年來又持續開發了高氮釩氮合金制備、釩氮合金品位穩定控制等一系列原創性關鍵技術。釩氮合金兩化融合示范線建成投用后,不僅產線用工優化22%,而且所生產的釩氮合金具有氮含量高、品位穩定、表觀密度高等特點,產品暢銷國內外市場,深受顧客喜愛。2022年11月,攀鋼釩鈦的釩氮合金產品獲評為工信部、中國工業經濟聯合會聯合發布的“制造業單項冠軍產品”。
同時,攀鋼釩鈦股份將釩氮合金兩化融合示范線建設的成功經驗應用推廣到旗下攀鋼集團西昌釩制品科技有限公司智慧工廠一期、二期建設,有效解決了釩產業制造流程長、工藝機理復雜、工序斷點多等諸多難題,實現了工廠生產態勢感知與運營一體化智慧管控等,獲評為中國軟件行業協會2024年度中國企業數字化創新應用場景。
數字化智能化技術的成功應用,為攀鋼帶來了一系列的實績和榮譽,讓攀鋼釩氮合金生產由“人工制造”邁向了智能制造,也讓攀鋼釩氮產品生產“挺直腰桿”。
【編·語】
開釩氮合金數字化生產之先河
樊三彩
國內的釩氮合金生產目前仍以傳統生產方式為主,作為首條釩氮合金數字化生產線,意味著沒有任何過往經驗可借鑒,在全國50多家釩氮合金生產企業中,攀鋼成為“第一個吃螃蟹”的企業。
成為開先河者,就要系統地解決很多問題,敢于打破諸多常規,包括可預測和不可預測的問題,難度不小。首要難題就是確立科學的建設模式。要大規模改造這條國內首屈一指的年產8000噸釩氮合金生產線,需要在不影響生產的情況下實現升級,這個過程尤其需要精心設計、小心協調,即使在有規劃圖的情況下,也要隨時準備應對計劃之外的情況。例如,一次篩分接料裝置(篩分機與料斗的銜接部分)起著將篩分后的料球緩沖并送入料斗的作用。最初的設計是一個螺旋形滑梯結構,但安裝后發現它達不到預期的效果,要么料球不往下滑,要么滑下去速度太快導致碰碎。在現場,通過生產方和設計方集思廣益、共同努力,最終采用了逆向旋轉的斗提結構,完美解決了問題。
除了生產管控層面的難題,攀鋼在數字化工藝、技術研發上也敢為人先,實現完全自主研發。以混配料模型為例,配料的比例原本只能保密進行,現在則需借助模型,這對于企業商業機密的保護提出了極高要求。攀鋼最終通過簽訂保密協議、技術人員和工藝人員協同研發等方式確保了模型的成功開發。在推板窯模型的設計上,要實現遠程數字化集控,就要對窯內生產情況進行實時監控。攀鋼通過精準收集數據、調適設備連接方式,將窯內各部分溫度、壓力、流量等參數以及坩堝運轉過程等以三維可視化的形式綜合展現,并開發實現統計功能,實現對窯內情況的精準仿真模擬,變“黑箱”為“白箱”,打造了推板窯場景下的“黑燈工廠”。
作為釩氮合金數字化生產的先行者,攀鋼敢于突破、敢為人先的創新精神,問題導向、獨立自主的探索能力值得業內很多企業學習借鑒。
《中國冶金報》(2024年09月24日 04版四版)