近日,由中冶京誠總體設計的河鋼張宣科技氫能源開發和利用工程示范項目經過安全、順利、連續生產,產品高純直接還原鐵金屬化率已穩定在94%以上,各項指標達到國際一類標準,標志著全球首例120萬噸氫冶金工程示范項目一期工程圓滿成功,也標志著我國鋼鐵行業由傳統“碳冶金”向新型“氫冶金”的轉變邁出顛覆性、示范性、關鍵性步伐,開啟了鋼鐵行業綠色、低碳、智能化發展新紀元。
從2021年5月10日開工建設,到2022年12月16日全線建成投產,這項由河鋼集團與意大利特諾恩(TENOVA)聯手中冶京誠共同研發和建設的全球首例120萬噸氫冶金工程示范項目一期工程,在河鋼集團張宣科技建成投產,為世界氫能綜合利用解鎖了新應用場景。該工程在全球首次采用了以焦爐煤氣為還原氣體的高壓豎爐零重整氫冶金技術,工藝氣體中氫碳比高達8∶1以上,產品——綠色高純直接還原鐵金屬化率達到94%以上,達到國際一類標準;比同等高爐長流程生產每年減少二氧化碳排放達80萬噸,減排比例達到70%。中國鋼鐵工業協會在給其的賀信中指出,這是氫冶金核心關鍵技術創新的重大突破,是中國鋼鐵史乃至世界鋼鐵史上由傳統“碳冶金”向新型“氫冶金”轉變的重要里程碑,引領鋼鐵行業邁入“以氫代煤”冶煉“綠鋼”的時代。
走近全球首例120萬噸氫冶金工程示范項目,可以看到在其背后,是重構用能體系的突破桎梏,是勇闖創新無人區的責任擔當,是智能化建設先行的集智聚力。
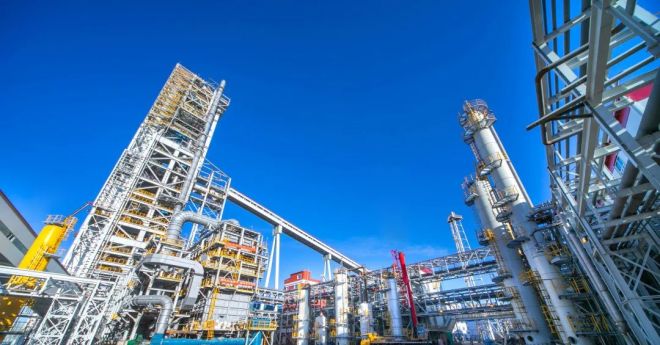
重構用能體系——
打破鋼鐵碳減排的天花板
近年來,氣候變化成為全球持續關注的焦點,各國都致力于推進碳減排行動。作為被重點關注的碳排放大戶,傳統鋼鐵行業面臨著越來越嚴峻的碳減排任務。傳統鋼鐵生產的能量載體主要來源于碳元素,所以鋼鐵工業的氣體排放物主要是碳氧化物。從全球范圍看,2022年,全球鋼鐵工業碳排放量約為28億噸,占全球能源系統排放量的8%左右,中國鋼鐵工業碳排放量貢獻了全球鋼鐵碳排放總量的60%以上,占全國碳排放總量的15%左右,是我國制造業領域中碳排放量最多的行業??梢?,鋼鐵行業的碳減排任務十分艱巨,推進鋼鐵工業降碳是我國“雙碳”目標實現的重點關注領域。而經過多年發展的我國鋼鐵工業的生產技術已經達到世界一流水平,以提高碳素能源利用效率為核心的節能降碳空間已趨于微小,意味著通過傳統工藝技術創新促使高爐長流程生產大幅度降碳已幾乎觸碰到了天花板。
2023年5月17日,歐盟碳邊境調節機制(CBAM)正式生效,意味著鋼鐵、水泥等多個行業將被征收“碳稅”。根據預測,我國鋼鐵行業出口成本或增加4%~6%,粗算為2億~4億美元。同時,鋼鐵下游行業也越來越關注鋼材產品的碳排放量,如奔馳、寶馬等汽車企業已經要求鋼鐵供應商提供汽車板產品的生命周期評價報告,并提出“綠鋼”要求。這意味著,如果不能盡快降低鋼鐵工業的碳排放量,不僅將會通過“碳成本提升”直接影響鋼鐵產品的國際競爭力,還會通過“碳足跡”影響下游制造業和建筑業的綠色發展。因此,鋼鐵生產要實現突破性碳減排,必須要從能源這個源頭入手。重構鋼鐵生產用能體系,這個不破不立的新理念,為打破冶金低碳減排的天花板指明了新方向。
近年來,氫能作為一種綠色、清潔、高效的二次能源正在加速發展。如果鋼鐵生產實現“以氫代碳”的能源轉換,將從源頭上大幅降低碳排放,甚至可以實現鋼鐵生產的“凈零碳”排放。冶金還原反應原理反映出,氫氣是一種很好的高效還原劑。氫氣擴散速度約為一氧化碳的4倍,其還原產物水的擴散速度約為二氧化碳的1.5倍,所以氫氣能夠比一氧化碳更快地通過礦石細微的孔隙達到反應界面,還原后生成的水蒸氣也比二氧化碳擴散得快。氫氣不但本身具有還原作用,而且對一氧化碳還原具有催化作用??梢姡瑲溥€原比碳還原的效率更高,且氫氣還原產物是水,沒有溫室氣體產生。鋼鐵生產如果使用“氫還原”替代“碳還原”,既可以省去燒結、煉焦等重污染工序,其產品——直接還原鐵又能補充我國廢鋼資源不足,為高質量鋼材提供優質純凈鐵,是電爐生產高端優質鋼和特種鋼的純凈原料,進而提高我國高端綠色低碳鋼鐵產品的國際競爭力。
勇闖創新無人區——
引領世界鋼鐵工業綠色發展的顛覆性變革
為了有力抓住重構鋼鐵生產用能體系的發展機遇,中冶京誠攜手河鋼集團著手探索將氫能用于鋼鐵冶金生產流程。但發展氫能冶金,必須解決兩個前提。
一是必須有豐富且廉價的氫氣資源。氫能是一種二次能源,不像煤、石油和天然氣等可以直接從地下開采,必須通過一定的方法利用其它能源制取。由于資源和能源稟賦,目前我國主要通過化石燃料制氫,主要在化工領域應用。作為鋼鐵聯合企業來說,焦化工序不僅可以為高爐提供優質的焦炭,而且其副產品——焦爐煤氣含有60%左右的氫氣。對氫冶金來說,焦爐煤氣無論是從供應規模,還是經濟性上都能很好地滿足氣源需求。不過,這是根據現有資源和能源稟賦采用焦爐煤氣制氫,只是過渡。張宣科技120萬噸氫冶金工程示范項目一期工程為未來實現100%綠氫豎爐直接還原打下了基礎。未來,隨著分布式能源發電及核電行業發展,制氫技術將快速進步,相關機構預測在2025年~2030年,大規模廉價的氫氣將大量應用于全社會,為未來氫冶金發展提供穩定的氣源供給。
二是必須開發一整套流程和設備作為工藝載體。近代鋼鐵工業已經發展得相當成熟,目前國內外成熟的工藝主要包括高爐、熔融還原、煤基和氣基直接還原等,其中高爐工藝主要使用以焦炭和煤為主的碳熱還原體系,熔融還原和煤基直接還原工藝雖然可以沒有焦化和燒結等工序,但仍然是以煤炭為能源的碳冶金。這些工藝即使可以實現局部富氫噴吹,但從本質上無法改變碳冶金的屬性。成熟的氣基直接還原工藝主要集中在北非和中東地區,采用天然氣為氣源,天然氣經重整后得到氫氣和一氧化碳的混合氣體進行還原煉鐵,從原理角度是最接近氫冶金理念的。因此,要實現“以氫代碳”的能源重構,選擇氣基直接還原為工藝載體符合氫冶金工藝的創新需求。
在解決了氣源和確定了工藝流程后,2019年11月22日,“關于河鋼集團與意大利特諾恩(TENOVA)聯手中冶京誠共同研發和建設全球首例120萬噸規模的氫冶金示范工程”的重大事件進行了首次公開發布,并確定河鋼集團全球首套氫冶金項目旨在采用焦爐煤氣“自重整”制氫,生產綠色高品質的直接還原鐵。其基本路線為:從分布式綠色能源、低成本制氫、焦爐煤氣凈化、氫冶金、成品輸送、二氧化碳脫除等全流程進行創新研發,探索一條世界鋼鐵工業發展低碳,甚至“零碳”經濟的最佳途徑,從改變能源供給結構入手,徹底解決鋼鐵冶金過程中產生的環境污染和碳排放問題,引領鋼鐵冶煉工藝的綠色、低碳變革。
以智慧驅動生產——
推動氫冶金工程
全面實現綠色智造和智造綠色
今天,河鋼集團在現有設計成果的基礎上,基于數字孿生技術,正在建立氫冶金智能控制系統數字模型,將產線“克隆”到云端,打造新一代智能管控模式,樹立全生命周期運營管控新理念。
其實,在該項目建設之初,中冶京誠與河鋼集團就為全廠設計注入了數字化基因,依托氫冶金的編碼體系,結合中冶京誠BIM(建筑信息模型)設計經驗打造鋼廠的數字孿生體。目前,中冶京誠與河鋼集團正努力構建國內首套氫冶金全生命周期數據編碼體系,為實現工廠級、車間級、設備級數字孿生的全面應用奠定基礎。該項目以“一張藍圖管到底”為基本思想,實現氫冶金全產線從設計、建設到運行的全生命周期智能化管理,形成全業務系統多源數據融合應用方案,且數出同源,為全廠生產、質量、能源、環保、安全、設備的管控提供統一平臺,實現一體化管控。該項目的主要思路是以自動化、信息化、智能化、數字化為指導路徑,以數字孿生成熟度模型為評價標準,構建全球首例氫冶金智能應用,實現涵蓋全工藝流程、全生命周期、全業務系統的智慧化管理。
一是以設計為先導,以虛仿實。依托中冶京誠BIM設計成果,結合數字孿生技術,為企業搭建集工程設計和設備設計于一體的數字化協同設計平臺,并對整個產線進行模擬和仿真,為氫冶金提供安全高效的數字化解決方案。
二是以交付為根基,以虛映實。搭建氫冶金工程數據中心,匯聚設計、采購、施工全過程信息,構建以“對象”為核心的“網狀”數據結構,打造企業資產數據庫,實現工程建造全生命周期信息(如設計、采購、制造、施工、安裝和調試)的集中存儲,節省設計、施工全過程時間,提高建設效率。
三是以智控為血脈,以虛控實。建設了基于艾默生公司DeltaV系統的DCS(分散控制系統)及SIS(安全儀表系統)系統,實現產線的自動化運行,并為產線穩定運行筑起了一道安全屏障;建立了加熱爐、換熱器、預熱器、冷卻和清潔、壓縮機、燃燒、冷卻塔、豎爐、外部冷卻器等全套數字模型,通過實時數據和模型計算,實現智能化控制,助力企業打造無人化、少人化生產場景。
四是以數據為大腦,以虛預實。打造鋼企信息化架構,建設了ERP(企業資源計劃)系統、產銷系統、實時數據采購系統、設備管理系統等,全面融合生產、質量、能源、環保、安全、設備數據,結合大數據分析和人工智能技術,實現精準智慧決策,向著以虛預實的方向不斷前進。
“氫”啟綠色,“智”聯世界,“能”創未來。中冶京誠與河鋼集團將進一步助力氫冶金工程向著虛實共生的綠色智能化方向不斷前進,將河鋼集團張宣科技打造成為世界一流的綠色、低碳、智能的氫冶金短流程示范企業,并以國家冶金技術進步為己任,不斷深耕氫能與鋼鐵的融合創新,驅動形成新的鋼鐵生態產業鏈條,為鋼鐵行業轉變能源結構、實現工藝革命提供全新路徑和創造全新場景,走出一條具有中國綠色智造特色的可持續、高質量發展道路。(趙志龍 楊永強 王東 李全鋼 貢金鵬)
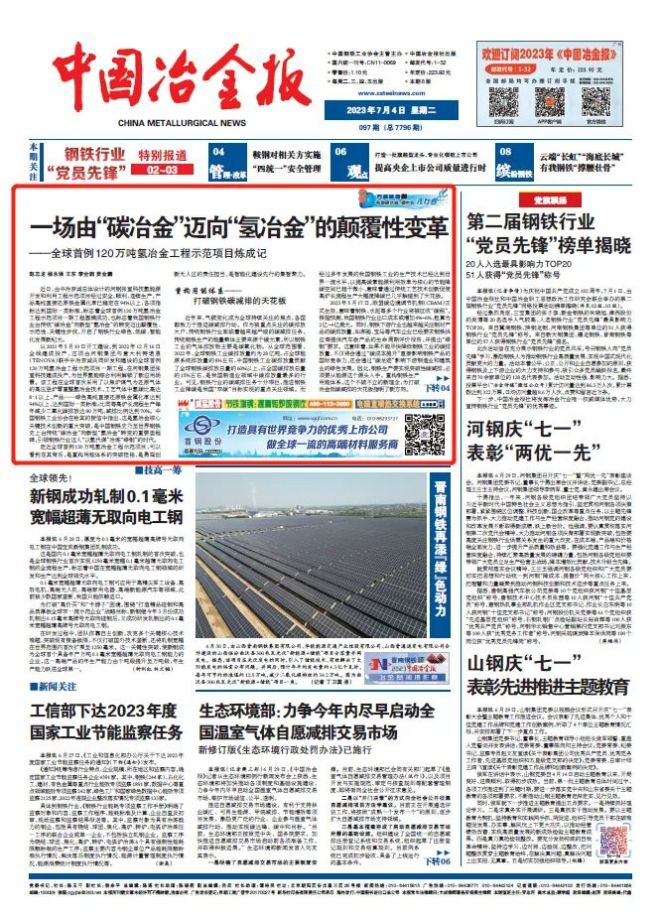