近日,由河鋼、東北大學、張宣科技聯合申報的《全氧富氫低碳還原熔化煉鐵系統及煉鐵方法》獲國家發明專利授權。
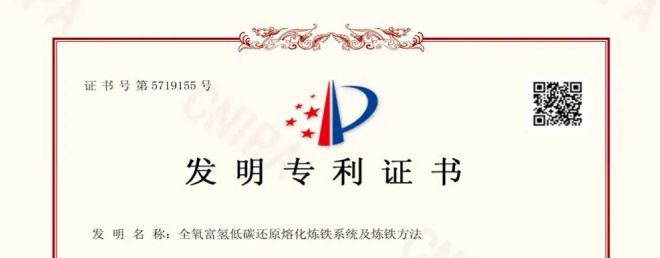
《全氧富氫低碳還原熔化煉鐵系統及煉鐵方法》發明專利,是全球首例富氫氣體(焦爐煤氣)零重整豎爐直接還原氫冶金示范工程(以下簡稱河鋼氫冶金示范工程)研發建設中總結提煉的實質性創新成果。該專利屬于氫冶金低碳煉鐵技術領域,可大幅度降低煉鐵生產中碳的使用量和減少CO?的排放量。通過設計相應的爐型及工藝,使間接還原區金屬化率達85%—95%,大大降低了噸鐵冶煉碳耗。采用全氧使自身反應器還原產生的煤氣循環利用,達到降低40%以上CO?排放的目標。
氫能被視為21世紀最具發展潛力的清潔能源。
作為鋼鐵行業綠色轉型的先行者,河鋼深耕氫能與鋼鐵的融合創新、協同發展,超前跟蹤世界氫冶金技術的研究與發展,以河鋼氫冶金示范工程為支撐,深入開展以焦爐煤氣為還原氣體的技術研究和產業化實踐,不斷攻克氫冶金技術壁壘,研發形成關鍵共性核心技術,構建氫冶金自主知識產權集群。

河鋼全球首創的“焦爐煤氣零重整豎爐直接還原”工藝技術,是河鋼氫冶金示范工程的核心內容。河鋼結合自身實際,充分發揮豐富的焦爐煤氣資源優勢,打破國際上采用天然氣制備原料氣的常規,創新采用焦爐煤氣作為氣基。
作為可以直接利用的氫能源,焦爐煤氣含有55%—65%的氫氣成分,可在氫基豎爐內催化裂解為一氧化碳和氫氣,實現“自重整”。自重整后,工藝氣體中的氫碳比可達到8:1以上,是目前工業化生產中含氫比例最高的氣基豎爐直接還原工藝,最接近未來100%氫還原的工藝狀態。同時,河鋼氫冶金示范工程豎爐反應器針對高比例氫含量進行了優化設計,預留了綠氫切換功能,不需大規模改造即可直接開展切換為更高比例富氫還原氣、純氫作還原氣的工業試驗,為未來實現100%綠氫豎爐直接還原提供基礎。
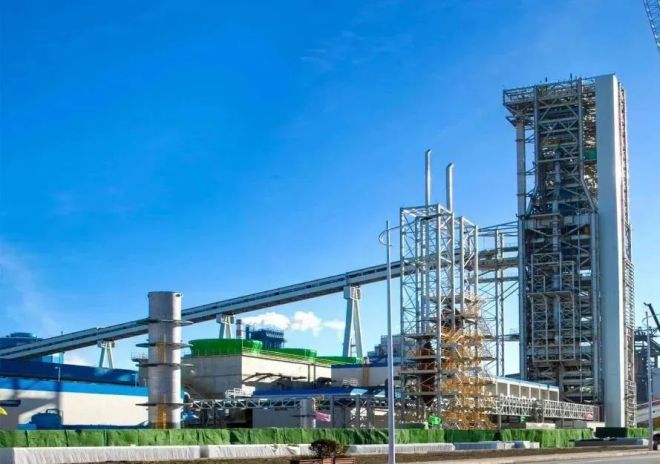
此外,河鋼還研發出具有國際領先水平的“CO?捕集+CO?精制”技術,可明顯減少整個工藝過程中的CO?排放量,實現CO?變廢為寶、增值創效;形成了包含《全氧富氫低碳還原熔化煉鐵系統及煉鐵方法》《控制氮氣富集的氣基直接還原煉鐵方法及系統》等30項氫冶金專利技術的綠色短流程工藝。
河鋼通過打造可推廣、可復制的“零碳”制氫與氫能產業發展協同互補的創新發展模式,進一步引領鋼鐵冶金工藝綠色低碳新發展,為我國鋼鐵行業實現由“碳冶金”向“氫冶金”的顛覆性變革貢獻力量。