完成人
李 麒、李世平、楊大雷、樊建成、劉 珧、陽建宏、李 杰、朱獻忠、郭 亮、趙 剛、龔敬群、羅云東、劉 晗、徐 鋼、王建宇
完成單位
寶武裝備智能科技有限公司、寶山鋼鐵股份有限公司、寶武集團中南鋼鐵有限公司、廣東韶鋼松山股份有限公司、北京科技大學、上海金藝檢測技術有限公司
立項背景
上個世紀,寶鋼引進、消化及完善點檢定修制,持續引領中國設備管理水平30余年。
在高質量發展的今天,設備數據在線率不足1%、定性點檢標準占96%、周期檢修項目占70%以上、點檢人員配置居高不下、能源環保壓力高企等,表明以點檢定修制為代表的設備運維技術發展遇到了瓶頸。
國內外鋼鐵同行也進行了設備運維發展的探索和實踐。如美國大河鋼廠,建立基于云的超級計算服務,安裝超過5萬個傳感器,探索預知維修。新日鐵住金引進人工智能數據分析平臺(DataRobot)提供云計算的合并數據分析環境,提高設備維護效率。新日鐵名古屋制鐵所在線監測的設備1253臺,監測的結果為制定檢修計劃和內容提供直接依據。三一重工以工程機械為對象,開展全生命周期運營管理,運用實時監控與分析、設備故障維修、預測性/預防性維護等,單臺設備潛在提升收入可達10%-50%。
從技術發展現狀來看,基本是在某類設備或某條生產線上的點狀智能化應用,尚未實現全流程、全工序、跨地域、跨空間的廣泛、深度數智應用。
鋼鐵企業從設備連接維度存在設備感知手段薄弱、高頻數據處理困難、多源多維數據難融合、信息孤島眾多等問題;在預警診斷和決策上存在狀態識別效率低、診斷準確性差、劣化趨勢無法把握、維檢決策可靠性低、經驗轉化知識困難等問題;在同類設備、同類產線設備運維對標中存在設備術語不統一、故障描述不一、設備顆粒度不一、設備表征數據無序、數據處理差異大等問題;現有的設備運維方式不支持智能運維的大范圍推廣應用,也缺乏智能運維的人員隊伍。
解決上述問題是一項極具挑戰性的復雜系統創新工程!
關鍵技術和創新點
本項目認為設備運維從“感官判斷、經驗決策”向“數據判斷、知識決策”的轉化是設備智能運維的核心。本項目以此為總體思路開展設備智能運維技術的系統創新。
圍繞設備智能運維,形成了以一個平臺、一個專家系統、一套標準化體系為核心技術架構、面向鋼鐵全流程的智能運維體系為載體的技術路線,共有四方面技術創新內容(見圖1):
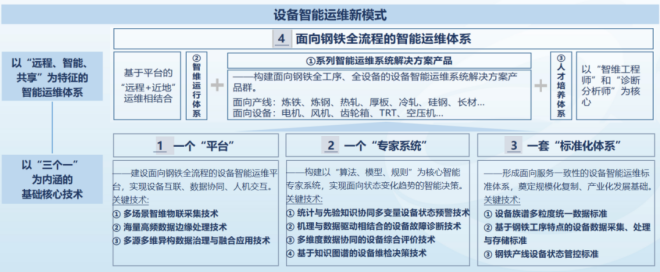
圖1 設備智能運維
創新點1:面向鋼鐵全工序的智維云平臺
面向鋼鐵全工序的設備智能運維平臺。平臺支持海量設備聯接,以‘云-邊-端’架構設計,支持智維生態協同、數據流動與知識創新賦能(系統架構見圖2)。涉及關鍵技術較多,其中3項尤其具有行業特色和創新性。
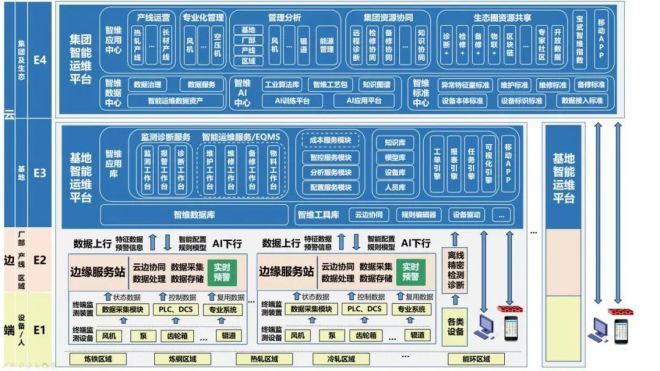
圖2 設備智維云架構圖
1.多場景智維物聯采集技術
針對鋼鐵設備數采場景復雜,環境高溫、高濕、多粉塵,設備種類多差異大等特點,研發和應用了一批專用智能數據采集裝置和大規模應用的低成本傳感器滿足了鋼鐵工業設備多場景數據采集需求;并通過多種物聯網絡通道技術融合研究,解決復雜環境下數采“最后一公里”問題。
2.海量高頻數據邊緣處理技術
鋼鐵設備數據量大,但數據價值密度低。通過研發系列算法和數據處理工具,在邊緣端運用高頻并發計算、工業特征工程等系列技術,解決了數據清洗、處理、特征提取問題,實現邊緣快速降頻、實時計算應用。同時開發系列無代碼、可視化編程工具,實現現場高效人機交互,解決了現場邊緣側海量高頻數據的傳輸、清洗、處理問題。
3.多源、多維、異構數據融合應用技術
設備數據呈現異構、多源、多維的特點,難以綜合應用。項目應用了CMDB技術來構建設備BOM及主數據,采用TSDB和集中分布式大數據Hadoop技術來處理海量實時動態時序數據和工藝控制數據,采用MongoDB處理半結構化數據,通過流式計算平臺對數據進行歸一化、校對,構建智維知識圖譜來實現維護經驗建模,通過研發工業數據融合技術實現了設備多類數據包容處理,使得設備數據得以跨設備、跨系統、跨產線應用。
創新點2:面向狀態變化趨勢決策的智能專家系統
構建面向狀態變化趨勢、人機協同的專家系統。以系列算法、規則、模型為核心,實現狀態識別、故障定位、維檢方案推送、結果驗證閉環、知識提煉匯聚的全過程決策智能化(見圖3)。涉及4項關鍵技術。
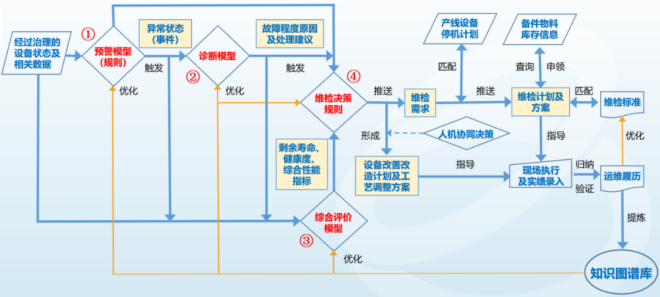
圖3 智維數據流程圖
1.統計與先驗知識協同的多變量設備狀態預警技術
針對設備狀態個性化發展變化的特點,結合對設備機理的理解,建立設備狀態動態數據統計模型,根據不同工況的狀態數據訓練出報警閾值,實現自適應綜合預警。不但支持各類閾值類報警,還支持趨勢報警,及包含工藝邏輯的邊緣規則預警,實現復雜場景、多變量耦合等情況下的異常狀態綜合預警。
2.機理與數據驅動相結合的設備故障診斷技術
面向鋼鐵設備復雜工況、負載多變、狀態變化耦合因素多、表征非線性等特點,利用算法工具將經驗數據化,將先驗知識納入模型,再結合大數據技術應用,提高案例學習效率,加速設備診斷模型的開發與調優,最終實現故障診斷的智能化、精準化。
3.多維度數據協同的設備綜合評價技術
融合設備屬性、運行狀態、工藝過程、維檢過程、運維履歷、同類故障特征、負荷累積等多維度數據,結合AI算法、專家經驗知識,動態調整非線性權重系數,形成設備綜合評價系統模型,對設備健康度及相關性能指標作出綜合性評價。
4.基于知識圖譜的設備維檢決策技術
通過多種維檢決策知識圖譜的開發與迭代,指導異常事件與維檢需求邏輯關系的梳理,形成維檢決策規則,嵌入平臺運維決策環節,推送最優的維檢對策,提高維檢項目的針對性、有效性。
創新點3:面向服務一致性的設備智能運維標準體系
將單一基地的個性設備技術轉變為全行業的工序共性技術,實現了設備數據與技術規范的一致性、解決了設備運維過程的數字化閉環,實現同類設備、同類產線統一標準、統一管理。涉及3項關鍵內容。
1.設備族譜多粒度統一數據標準
解決設備名稱不統一、設備故障原因描述各異、設備粒度不一、設備表征數據無序等問題,實現設備術語統一、顆粒度統一、數據表征統一。
2.基于工序特點的設備數據采集、處理與存儲標準
規范了設備數據的采集和處理過程,解決了同類設備之間數據互理解和互操作問題。
3.鋼鐵產線設備狀態管控標準
解決各鋼企設備運維標準不一、運維質量不一、檢修過程與驗證方法不一的問題,通過制定統一運維標準、運維質量評價標準、檢修與驗證標準,實現對多地域同類產線、同類設備高效一致管控。
創新點4:構建面向鋼鐵全流程的智能運維體系
為了最大限度釋放技術創新紅利,實現極致專業化基礎上的規模效應,項目也在業務流程和職業體系方面形成創新,包含3項創新內容。
1.面向鋼鐵全工序的智能運維系統解決方案群
依托寶武豐富場景和行業專家,形成了一系列面向鋼鐵全工序的智能運維系統解決方案,包括工序概況、智維目標、智維設計、監測技術應用、運維技術應用、全量數據應用、模型迭代升級等內容,具備了大規模、快速復制條件。
2.基于平臺的近地與遠程運維相結合的智能運維運行體系
以100%平臺預警、100%線上工作為目標,近地與遠程結合,前、中、后臺一體,依托平臺對多地域、同類產線、同類設備進行集中管控,所有管理在線、所有決策智能、所有資源共享,塑造全新智能運維運行體系。
3.以智維工程師與智維分析師為核心的智能運維人才培養體系
創新智維工程師、智維分析師為主體的智能制造新職業體系,并配套完善人才培養機制,為設備智能運維的可持續發展奠定人才基礎。
通過項目研究,形成標準11項(其中2項國家標準,9項企業標準),專利88件(其中授權發明專利18件,授權實用新型13件,在審查發明專利57件),軟件著作權9項,論文16篇,論著1部,覆蓋項目全部核心技術。
與國內外水平的比較
在鋼鐵行業和設備運維領域,通過對監測設備數、監測數據項、數據頻度、設備覆蓋率、預警、診斷準確率、覆蓋范圍、運維體系等方面進行對比分析,本項目智能運維整體水平為國際領先。
經成果查新,項目具有新穎性;中國金屬學會組織成果鑒定結論,項目成果達到國際領先水平。
創新效果
目前,項目成果已在中國寶武十五大生產基地及多元產業多家單位部署應用,并已擴展至集團外生態圈(如漣鋼、寧鋼、鞍鋼鲅魚圈等)。累計接入900余條產線、設備超33萬臺,計劃3年內接入設備超百萬臺,見圖4:
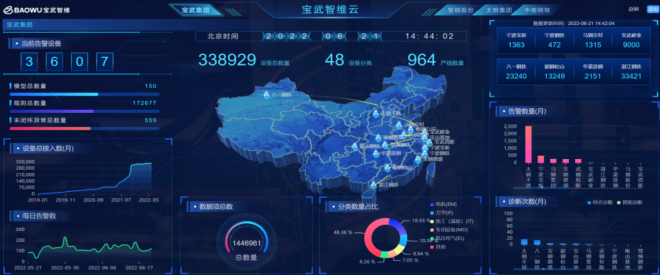
圖4 項目整體應用情況
在產線類設備上,已集中熱軋、高線、冷軋等數十條主產線。其中馬鋼2條熱軋集中管控后,21年產量創歷史最佳,產線故障時間為近3年最少;其他產線集中管控后也分別取得良好效果;隨著同類產線數量增加,設備資產效率、人事效率和管理效率將大幅度提升。
在通用類設備上,以風機為例,近5000臺風機集中管控后預警和診斷準確率均超90%,點檢負荷、檢修負荷持續下降近三分之一,隨著同類設備數量增加,規模效益更為可觀。
項目直接經濟效益達到5.4億元(項目成員單位內),間接效益17億元。實現了超大規模的工程化應用,項目相關技術為鋼鐵行業設備運維的轉型變革提供了堅實的理論基礎和技術保障,具有完整知識產權,關鍵技術自主可控。
我們愿與所有鋼鐵人一起,共同推動、共同進步,積極打造智能運維生態系統(見圖5),讓智能運維成為鋼鐵行業設備管理的中國創造。
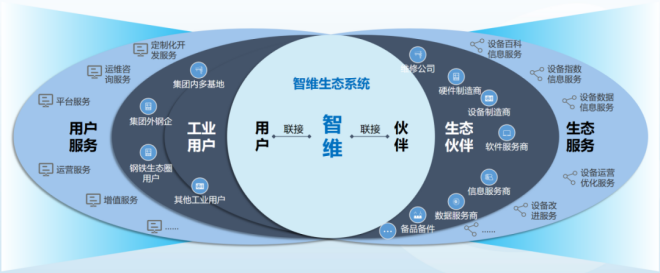
圖5 智能運維生態系統