5月25日-27日,德龍鋼鐵組織5項創新成果參加了“河北省第六屆質量創新成果發布會暨經驗交流會”,經過現場展示以及專家評審,5項成果從參加交流的136項成果中脫穎而出,全部獲得一等成果,其中“230㎡燒結機點火技術創新”項目獲得質量創新類項目最高分,充分體現了德龍鋼鐵的質量創新能力。
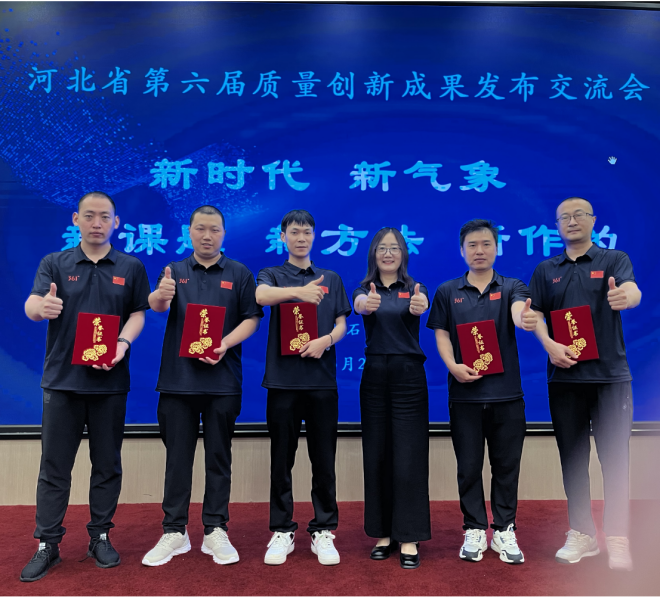
近年來,德龍鋼鐵高度重視質量管理與創新改進工作,一方面實行“3維”+“六化”+“標準化”質量管理模式,加強進出廠質量把關,嚴抓過程質量控制,緊盯標準化操作規范;另一方面,積極結合各生產單位組織開展管理創新與技術創新,圍繞公司發展目標要求,以車間班組為單位,以科技創新為導向,以創新為出發點,開展了一系列的QC小組活動、工藝優化、問題攻關以及課題研發創新等活動,為公司提質降本做出了重要貢獻。
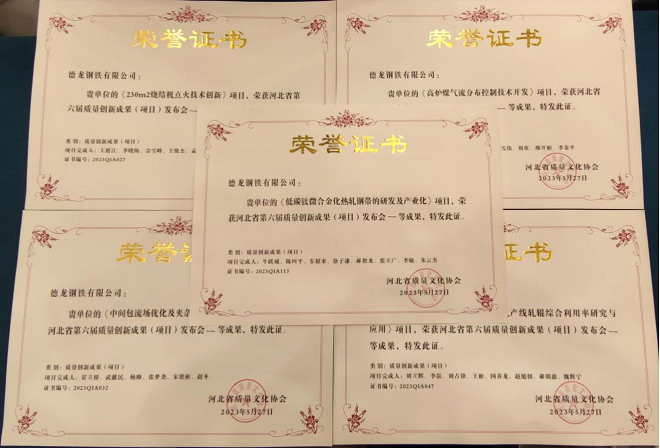
其中,燒結廠“230m2燒結機點火技術創新”項目,通過建立風溫、氧濃度、空燃比多目標協同控制點火體系,開發燒結火焰前鋒和燒結配碳量綜合匹配技術,點火溫度范圍由下降±3.5%,燒結點火能耗由4.19kgce/t降低到3.04kgce/t,改善了燒結點火質量,降低了燒結點火能耗,活動期間合計創效375.41萬元。
煉鐵廠“高爐煤氣流分布控制技術開發”項目,通過建立爐料顆粒運動及料面分布數學模型,開發高爐串罐式無鐘爐頂的局部三維布料模型以及上下部優化匹配控制,煤氣利用率達到了43.74%以上、燃料比完成528.86kg/t,年創效達到2100萬元以上。
煉鋼廠“中間包流場優化及夾雜物去除模擬研究”項目,通過以“基于氣幕擋墻技術的中間包流場優化數值模擬”與“水力學模型物理模擬”的結論為導向,優化中間包結構布局以及吹氬透氣磚等控流裝置,控制鋼液流動方向和滯留時間,實現了SPHC鋼鋼中單類夾雜物≥2.0級比例由8.0%降低至6.2%,中間包平均使用壽命達到24.6小時,過鋼量增加了600t/包,噸鋼耐材費用降低了0.46元/t鋼。
軋鋼廠“基于高效軋制的熱軋產線軋輥綜合利用率研究與應用”項目,圍繞軋輥再制造修復循環使用和舊軋輥原地強化使用兩個方面,以成分優化和性能強化為核心出發點,運用正交試驗法、PDCA循環、失效分析、風險管控等質量管理工具,通過選用合理軋輥材質,應用軋輥表面修復和強化技術,實現了軋輥使用性能提升與成本降低,其中,精軋支撐輥掉肩量減少了75%,支撐輥服役周期延長了45%,軋輥消耗降低了0.055kg/t。
技術中心“低碳鈦微合金化熱軋鋼帶的研發及產業化”項目,通過開發低碳鈦微合金化鋼夾雜物控制技術、低碳鈦微合金化鋼鑄坯質量優化技術、低碳鈦微合金化鋼熱軋-冷軋-退火過程MnS夾雜與顯微結構協同調控技術,成功開發了低碳鈦微合金化熱軋鋼帶,產品合格率達到100%,月平均產量達到1.5萬噸以上,實現了產業化生產。
創新發展是當今高質量發展的主旋律。下一步德龍鋼鐵將繼續以質量創新為核心,以管理創新為驅動,推廣、總結質量創新活動中的典型方法和經驗,利用多種形式組織各層次員工積極參與改進,同時高度重視各種績效改進工具、方法的應用培訓,推進公司產品質量持續提升。(通訊員 劉立偉)